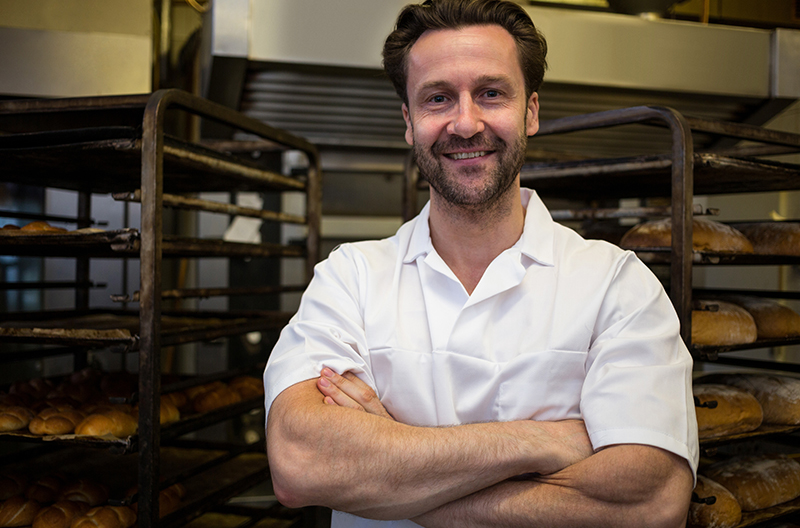
In the unique realm of food distribution, finding the fragile harmony between cost decrease and keeping up with item quality is a test that each distributor goes through. With increasing costs and price conscious customers, distributors need to continually adapt to stay successful.
In this blog, EasyVend will dig into useful and proficient practices that food distributors can take on to reduce expenses without compromising the quality of their items.
Let’s get into it!
Strong Inventory Management
Effective stock management is the foundation of decreasing costs in the food distribution industry. Keeping a reasonable stock level guarantees that you’re not tying up capital in that frame of mind while likewise forestalling stockouts that can prompt lost deals. Implementing technology like an Order Management System can help in exact automation of the entire stock management process. By streamlining processes using technology, distributors can limit costs without compromising on quality or service.
Build Relationship with Suppliers
Coordinated effort and correspondence with your suppliers are fundamental for cost reduction. Work intimately with your supplier to try to get better prices and terms on productions. Consider shopping around for other suppliers to seek a better price. Choosing the right suppliers will lead to better deals on product sourcing and will allow your distribution company to trade successfully.
Embrace Innovation
Integrating technology can fundamentally improve the effectiveness of food distribution tasks. Using solutions like an OMS can smooth out operational tasks like ordering, invoicing, customer payments reporting and more in one central software solution. The benefit of having an automated system is it reduces manual labor costs.
Implement Low-Cost Equipment
The energy usage of your business’ equipment can be a significant strain on expenses. To reduce costs, put resources into energy-effective tools and equipment. Consider using environmentally friendly power sources like sunlight-based chargers to control your offices, prompting long haul cost savings.
Quality Control Measures
Keeping up with item quality is non-debatable in the food distribution industry. Carry out severe quality control measures to guarantee that items satisfy or surpass industry guidelines. While it could appear to be illogical, putting resources into quality control forthright can set aside you cash over the long haul by decreasing returns, reviews, and client grumblings. Consistently assess approaching shipments and lead arbitrary quality checks to get any issues before they arrive at clients.
Employ a Strong Team
For distribution to be economical, cooperation and communication are required across the entire supply chain. Cooperate closely with other staff to hammer out better processes. A strong team will lead to more efficient and accurate operations which in turn will reduce the risk of costly errors.
Ongoing staff Training and Development
Following on from the point above, thoroughly prepared, and trained staff are an invaluable resource in any business activity. Give thorough preparation to your staff on how to complete tasks successfully, like order management, stock take etc. Engage them to recognise and report any issues quickly, forestalling expensive errors and decreasing the possibilities of item harm or deterioration.
Effective Packaging Solutions
Packaging plays a vital part in safeguarding the nature of food items during circulation. While it’s fundamental to safeguard items, consider utilising packaging materials that are financially savvy and harmless to the ecosystem. Right-sized packaging can limit waste and lower delivering costs.
Data Driven Decision Making
Use your business data to examine and pursue cost-cutting measures. No business is the same, stay on top of and understand what your data is telling you about your business. See what areas are performing well and what areas require improvement. Based on the data make informed decisions and the required changes to maximise profitability.
Final Word
In the profoundly competitive industry of food distribution, reducing costs is essential for ongoing success. The 8 tips presented are a few proven ways distributors can decrease costs quickly without compromising on quality.
We hope you enjoyed reading this article. To read more articles like this, please visit the EasyVend latest news page here.
About EasyVend,
For Supply Chain Businesses, EasyVend supports and automates every part of your business, freeing you up to grow your sales simply, unlike other ERP systems.
EasyVend includes key everyday features like Inventory Management, Online Ordering, Invoicing, Receipting, Automatic Credit Card Payments, Xero & MYOB Accounting Integration, Route Management, Business reporting and more.
Using the latest technologies, EasyVend removes common frustrations making business more streamlined today!
To learn more about EasyVend or to get a no-obligation free demo of the software, call us today on 1300 473 744 or submit the form below.